28 December 2020
Enabling Major Capital Projects with Digital Twin
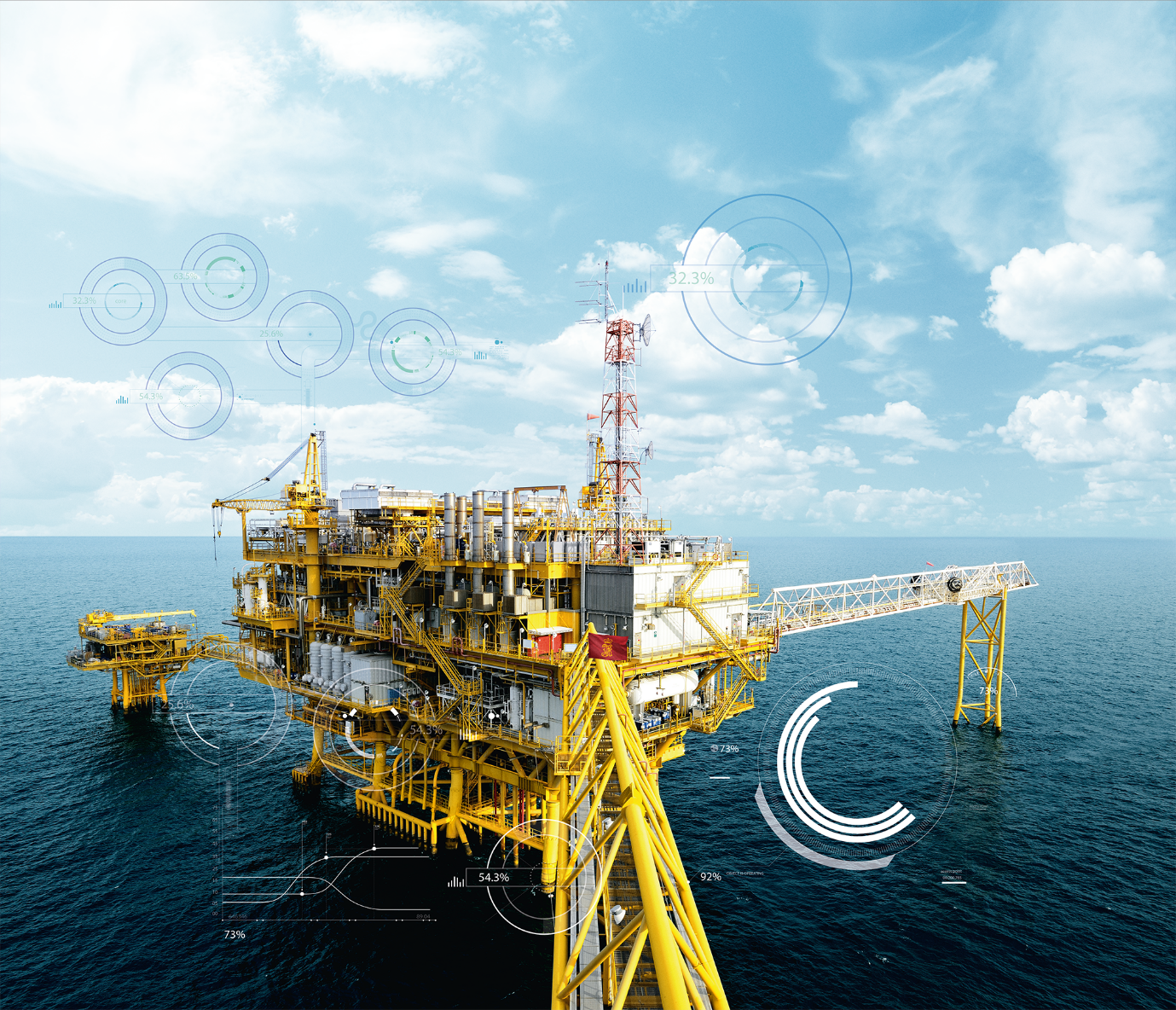
Kognitwin? Energy for Asset Development
Unify data, knowledge and people. Enable the best decision every time.
Traditionally, the management of projects and capital expenditure has been limited by functional siloes, human cognitive ability to integrate large amounts of information and complex system implementation reviews. As a result, the cross-functional collaboration necessary to prevent and overcome unforeseen challenges tends to be slow and costly in terms of project delays, increased cost and functional design limitations. The operational deployment of Kognitwin? Energy, along with advanced analytics and intelligent edge capabilities, can open the door to fundamentally different ways of planning and operating assets, leveraging enhanced collaboration, supporting intelligent decision making and increasing levels of automation.Time and cost savings strengthen the case for adopting Digital Twin during the development of a project. Time savings have been documented at up to 40 percent, reducing the time to complete an average offshore project from three years down to two. Total cost savings have been conservatively estimated at 10?20 percent of the total project cost.
Value of Kognitwin through the Stages
The early phases of asset development are critical. Concept evaluation, equipment selection, design validation are processes that can and should increasingly be the focus of optimization improvement. The later phases of project and asset development also present fantastic opportunities for business advancement.
Due Diligence
In today?s dynamic environment, it?s increasingly important to ensure that investments are diligently considered, and risk is minimized. The ability to simulate and study production performance, apply machine learning specifically trained on appropriate legacy data from previous projects and physical models in the Pre-FEED and FEED studies, can contribute to higher levels of confidence and reduced levels of risk profile of Major Capital Projects. Doing so can/will also reduce the level of effort required to come to a Final Investment Decision.Optimizing the decision-making process, improving internal workflows and creating repeatable procedures for teams to practice will reduce cost, scheduling and uncertainty as the project is developed over time.
Concept Evaluation
During Pre-FEED and FEED, a Digital Twin will assist with determining the feasibility of a project. Using the known data and existing equipment information, we can greatly optimize the cost of these studies, designing field lay-outs with increased efficiency and higher degrees of confidence for project success. Additionally, this process can be a catalyst for identifying existing design specifications and standardizing equipment, greatly reducing the demands for engineering, qualification and material specifications elements for the project (more on that later). All these things equate to reduced risk with known applications / proven equipment and lead to faster positive cash flow due to earlier first oil dates. Tooling requirements become standardized, easier to plan, maintain, etc.
Enhanced Collaboration
During the project execution phase, Digital Twin shines as a collaboration tool in addition to providing many other functions. The twin assists with design validation processes, project team visibility and workflows, data and document unification and project tracking KPI?s. The project engineering and systems integration team can simulate and visualize equipment configurations, communications protocol and controls through virtual commissioning solutions. Reduced design and engineering time with improved design quality through improved cross-discipline collaboration, results in fewer changes in later phases like construction, commissioning and installation.For example, in the early design phases for an offshore platform, the design engineer must take into consideration aspect such as material cost, subsea topography, well placement, flowline placement, etc. Without the appropriate tools or process, flow assurance is not necessarily prioritized or can be overlooked completely. But it doesn?t have to be, thanks to Kognitwin? Energy. Importing data and models into the twin allows for streamlined, multidiscipline reviews. Together with the reservoir engineer, design engineers can make sure that the wells are accurately located, moving the planned assets like pieces on a chessboard, but using simulations and integrated material requirement knowledge to output the ?what if? results. Working in collaboration, these normally independent teams can share and learn in a shorter amount of time, potentially avoiding costly time and mistakes.
Design Validation
Because the system can be fully simulated so early in the project, Operations and Maintenance philosophies can be developed well before any equipment hits the water. Tooling requirements, offshore scopes of work, number of personnel required (which could also be minimized by remote operations), vessel and schedule needs, etc can be planned for much earlier and much more effectively than historically done. It?s also worth mentioning that because these activities can be considered so much earlier, with standardized equipment, the likelihood of ?unforeseeable? or overlooked situations is greatly reduced, resulting in smoother commissioning and start- up activities.
Standardized Equipment
While there will always be specific requirements and specifications for production equipment depending upon reservoir characteristics, water depth, pressure and temperature constraints etc, there is a massive opportunity within the industry to standardize the equipment that is procured for major capital projects. The level of effort required for engineering, analysis, testing and qualification is a significant part of project costs. What if we could identify existing equipment specifications, plug and play with simulation to validate equipment, and make use of already existing part numbers for a development project.Standardizing equipment not only benefits the capital investment on the front end of the project, but it can pay dividends over the life cycle of multiple projects.Every time a new tree, or new manifold is designed, we have to recreate lifting procedures, reconsider splash zone dynamics, and installation procedures etc. Now, there will always be a level of analysis and review that has to be completed for these projects but there are significant opportunities for how we select equipment and design the layout for offshore projects.
Application for Best Practices
Modular construction
Streamlining projects with modular construction philosophies has helped lower cost and achieve faster results for operators. As the Digital Twin assists with standardizing equipment and overall design, incorporating Kognitwin with modular construction projects also bring visualization, design validation and reduces engineering costs while also streamlining process workflows. Cloud-based access and collaboration tools enable project agility and improved project performance.Construction and Fabrication tools can enable better access to specific instructions in the field which means more ?time on tools? and fewer errors.
Data & Document Unification
Utilizing a single source for information and breaking down operational and/or project silos increases the effectiveness in which decisions can be made. Having one platform where teams can view, edit and modify documents, in real-time while also collaborating regardless of geographical locations creates a modern approach to managing information.After project completion, document hand-off is almost already complete, short of any as-built or last-minute changes. The Kognitwin service platform serves as both the project portal and operational portal for documentation throughout the entire lifecycle of the asset.
Virtual Commissioning
Early Verification of Control and Operations Strategy improves start-up time and reduces complications. Kognitwin enables the ability to influence design changes before the final configuration is complete saving time and cost and avoiding unnecessary cost overruns related to commissioning and start-up. Schedule improvements can also be achieved. Installation and logistics plans can be developed through simulation and optimization exercises.
One Button Start-up
With One Button Start-up, the project team can design the control strategy and the set-up of automated sequences within the digital environment. Doing so enables the team to fully test and validate the sequences on the physical models, optimize control loops for energy efficiency and use the minimum amount of energy to start up the facility and operate it. This philosophy helps to ensure that start-up and commissioning processes are efficiently planned and executed without issue.The goal of the Digital Twin journey is to achieve true Operational digitalization for your team. Doing so adds layers upon the collaboration and efficiency already achieved through the project phase, bringing an improved operating model across your entire value chain. As the company embarks upon this initiative, it?s important to ensure that the destination is understood at the onset of the journey.Some of the values you can expect following installation and commissioning include:
Life of Field
Installation and commissioning procedures are re-written every time a system is designed. Understandably, as technology is improved and developed, we want to apply the right tech to our facilities. That being said, should we really have to recreate similar installation tools over and over again? Does each project really need its own service equipment? Our tools can and should be more universal.How do we apply smart design to smart service and down time? The answer is, the equipment should tell us. The serviceability of our assets shouldn?t be an afterthought. At the end of the day, we should enable ourselves to not only get a live view of asset performance remotely and in real-time, but also make the most out of the equipment designed to extend the life of the field.
Organization
As a new operating model is developed for your organization, opportunities will exist to restructure how you support your asset(s). Overall, the Kongsberg approach enables a Digital Twin which fits your organization and provides an enterprise-level platform that enables insights across the owner/operator?s asset portfolio. Your organization can leverage the availability of a true Centre of Excellence approach by providing all information in one location, regardless of geography. Headquarter roles can view KPI?s / metrics for comparison across geographies while managers and individual end-users can collaborate seamlessly across distance and job functions for efficient, effective business decisions.
Predictive Maintenance
With a leaner, more agile organization you can apply prediction models to forecast how degradation will develop and estimate remaining useful life (RUL) of main components. During normal operations you gain a full understanding of dynamic scenarios to improve planning and execution. Build on condition and operational data and utilize analytical tools to detect changes at system and component level. Integrate information for a similar type of systems and equipment throughout your entire portfolio to improve the quality of data and discover trends and failures across assets.What can be achieved is stabilized production, increased uptime and productivity. Your team can be prepared ahead of time, save time ramping up a complex dynamic operating regime by leveraging simulation. Finally, turnarounds, modification & improvement projects are more effective reducing the number of major operational events.
Health, Safety and Environment
Applying emerging technology for the energy industry of the future is what will differentiate operators? competitive advantage. Carbon emmissions reduction, safer work environments, reduced POB are all initiatives that are being driven today within the industry. Remote work, optimizing performance and predictive analytics enable these improvements from facility to facility through Kognitwin.
Summary
The importance of ROI and speed to market for investments is increasingly relevant in a volatile environment. By leveraging innovative solutions, adapting through the diligent adoption of emerging technologies and tapping into accessible value through digitalization, operators can reduce the time it takes for them get the product to market from the time they make a final investment decision and achieve first oil.The benefits of a smart facility, designed, validated and selected through data-driven and modern decision-making processes, paired with a true operational digital twin are extraordinary. And ultimately, it all means reduced downtime, improved oil recovery and extended life of field while also reducing the risk profile from both a performance/safety perspective as well as the investment perspective.
Miguel Valdez is a Growth Manager in the Digital Energy team at Kongsberg Digital. Based in Houston (USA), Miguel has over 10 years experience in the Oil and Gas industry managing aftermarket services in the deepwater oil and gas sector, major subsea capital projects around the globe and strategic business development.
Author
Morten Hansen
VP Marketing, Kongsberg Digital